SFS Laminate Nonwoven Fabric is an innovative solution for a wide range of medical applications that require a lint-free fabric. It is resistant to a variety of chemicals and binders, making it ideal for use in sterile environments. In addition, it is able to retain its strength and shape during processing. It also has the added benefit of being liquid-repellent, which prevents spillages and leakage.
A laminated nonwoven fabric is a special form of a blown, spunbonded or carded non-woven that incorporates an intermediate layer of a melt-blown olefin-type resin and is combined with an upper and lower covering layer made of spun-bonded or carded polyester-type non-woven fabrics. This allows the laminated fabric to have the softness, porosity and water resisting properties possessed by the melt-blown non-woven fabric, while at the same time providing strength, hand, touch and other advantages of the spun-bonded or carded polyester-type fabric.
Laminated nonwoven fabrics are produced by introducing an intermediate layer of a melt-blown non-woven olefin-type resin fabric between two covering layers of spun-bonded or carded polyester-type olefin or polypropylene non-woven fabrics, where the fibers of the spun-bonded and carded polyester-type non-woven fabric are bonded together locally and at a coarse density. When the melt-blown non-woven olefin-type emulsion is stuck to itself by heat embossing, there develop inconveniences nearly similar to those of when the melt-adhered portion of the melt-blown non-woven olefin-type fabric is joined to another material.
In the case of a wetlaid, airlaid or carded nonwovens, the staple fibers are first spun into a yarn which is then "opened" in a multistep process and spread in a uniform web in a wetlaid, airlaid, or crosslapping operation. The yarns or staple fibers are usually oriented in the longitudinal and transverse directions of the web, although they may be oriented randomly as well. The staple fibers are typically of a type such as polyethylene, polypropylene or polyester and may be mixed with other materials such as rayon, cotton and viscose (Fig. 1.9).
The laminated nonwoven fabric of the present invention can be produced by laminating an intermediate layer of a melt-blown or extruded nonwoven olefin-type resin cloth between an upper and lower covering layer of spun-bonded or carded polyester-type polyester or polypropylene non-woven fabrics. The staple fibers of the spun-bonded or carded fabric are inserted into the melt-blown or extruded nonwoven and intermingled with the staple fibers of the other covering layer, and then subjecting the laminated material to water-jet working, so that the fibers of the spun-bonded or carded non-woven fabrics are bonded locally and at a coarse density to the olefin or polypropylene based non-woven fabrics, thereby giving it a softness, porosity and water resistance characteristic of the melt-blown or extruded olefin-type resin fabrics. The fabric can then be used for a variety of purposes, including isolation gowns, surgical gowns, drapes and covers, bedding and clothing, food or grain packaging and shopping bags. The fabric of the present invention is easy to cut with any common slitting technique and can be punched as well.
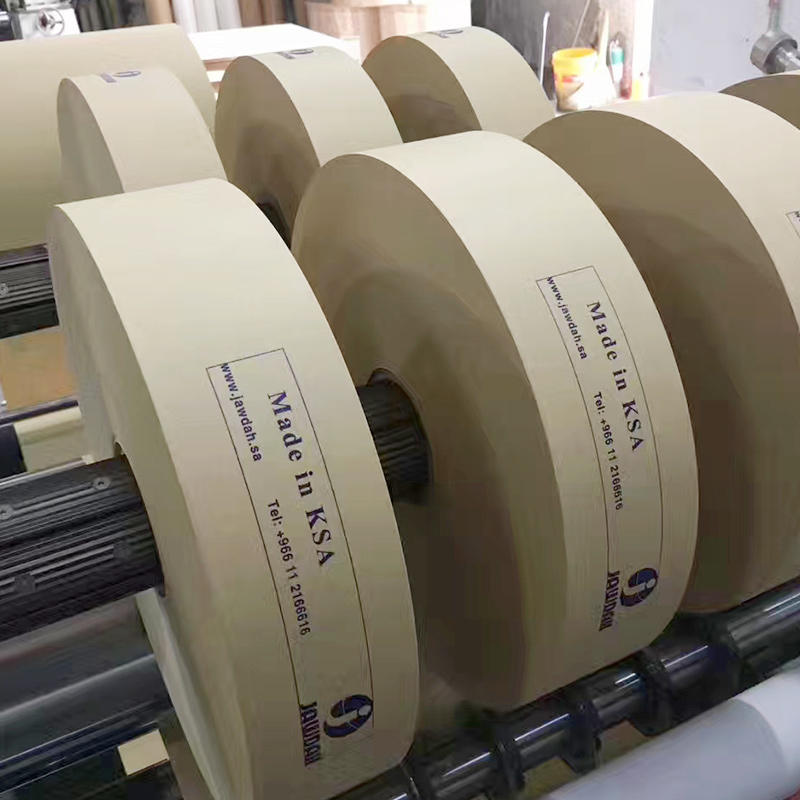